Nihonto
valmistamine
Kahjuks
pole meieni säilinud ülestähendusi iidsete Koto-perioodi
mõõkade valmistamise meetodite kohta, seetõttu
saame tänapäeval kõneleda vaid meetoditest, mida
kasutasid sepad alates Shinto-perioodi algusest. Kui Koto-ajastul
valmistati mõõgad reeglina kohalikust toorainest
ning koolkonnaspetsiifilistel meetoditel, siis Shinto-perioodil
metallitöötlusmeetodid unifitseeriti ning edaspidi sai
rääkida vaid ühest konkreetsest viisist, kuidas
valmistada jaapani mõõga jaoks vajalikku metalli.
Allpool olen kirjeldanud kaasaegset terasevalmistusmeetodit, kuid
sellegipoolest on tegu täiesti traditsioonilise meetodiga
– kaasaegne meetod on ainult mõnevõrra loodussõbralikum.
Tatara
Traditsioonilise jaapani mõõga terase tooraineks
on raudliiv, mida töödeldakse spetsiaalses saviahjus,
tatara’s. Kaasaegne tatara erineb traditsioonilisest vaid
selle poolest, et kaasaegses ahjus toimub õhu pumpamine
mootrite abil. Tegu on üsna kuluka ja suurt kogust toorainet
nõudva protsessiga, mistõttu tänapäeval
kasutatakse seda meetodit vaid mõõkade jaoks vaja
mineva terase valmistamiseks. Kaasaegsete terade, ehk shinsakuto’de
valmistamiseks vaja mineva terase tootmisprotsessi korraldab aastast
1977 Jaapani mõõgavalmistuse koordinatsiooni- ning
järelvalveorganisatsioon NBTHK, koostöös Hitatchi
Metals LTD’ga, paigas nimega Torigami, Shimane Prefektuuris.
Raudliiv kaevandatakse Chugoku mägedes, kus raudliiva kvaliteet
on Jaapani parim. Iga aasta valmistatakse ca 3-4 tonni terast.
Raudliiva sulatamiseks kasutatakse kivisöe asemel puusütt
– see võimaldab sulatada metalli madalamal temperatuuril
(umbes 1200-1500 C), nii välditakse rauakristalli laienemist
ning hapraks muutumist. Samuti aitab madal temperatuur vältida
ebapuhtuste (nt, fosfor ja väävel) sulandumist rauaga,
lisaks sellele on puusöe reduktsioonivõime märksa
suurem kui kivisöe oma, mis tähendab, et raudoksiidist
hapniku eraldamine ning puhta raua saamine võtab vähem
aega kui kivisöe puhul.
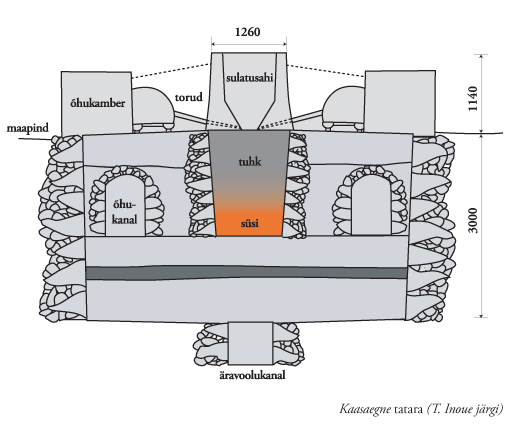
Tamahagane
Peale söe ja raudliiva asetamist ahju algab töödejuhataja
ehk murage juhatusel põletusprotsess, mis võtab
kokku aega 70 tundi. Ahju esialgne paksus 200-400 mm väheneb
protsessi käigus 50-100 mm-ni, ning 8-st tonnist raudliivast
ja 13-st tonnist puusöest saadakse lõpptulemusena
ainult 2-2,5 tonni terast, millest kasutuskõlblik on vaid
1,5-1,8 tonni. Peale sulatust saadaksegi ahjust käsnalaadne
metalliblokk, mis on 2,7m pikk, 1m lai ja 0,3m kõrge. Antud
bloki ehk kera väljavõtmisel muudetakse ka tatara
kasutuskõlbmatuks. Ühe kera valmistamise hind on tänapäeval
umbes 100 000 dollarit. Kasutuskõlblik teras tekib kahele
poole kera’t, kus tänu õhu pidevale pumpamisele
on oksüdatsioniprotsess olnud piisav. Antud terast kutsutakse
tamahagane’ks, ehk vääristeraseks. See teras on
oma keemiliselt koostiselt äärmiselt puhas võrreldes
isegi kaasaegse tööstusliku süsinikterasega. Protsess
leiab aset kesktalvel, teras jahutatakse jahedas väliskeskkonnas
ning seejärel jaotatakse ära ligi kolmesaja elukutselise
registreeritud sepa vahel.
Erineva
süsinikusisaldusega terasetükid, kuumutatakse ahjus
puusöe ja riisikõrte tuha abil. Seejärel taob
sepp tamahagane lamedaks ning purustab plaadi tükkideks,
seejärel asetab tamahagane tükid käepidemega plaadile,
katab need spetsiaalse riisipõhku ning savi sisaldavas
vees immutatud jaapani paberiga (et vältida pindmise terase
oksüdeerumist). Seejärel algab sepistusprotsess. Metall
taotakse lamedaks ning murtakse kokku kordamööda üht-
ning teistpidi (risti ja paralleelselt käepidemega) umbes
10-15 korda, saavutades nii vastavalt 1000 kuni 30 000 kihti.
Antud protsess, mida kutsutakse orikaeshi’ks, on vajalik
nii kõiksugu ebapuhtuste eemaldamiseks, süsinikusisalduse
tõstmiseks, kui ka terase struktuuri ühtlaseks muutmiseks.
Teisisõnu muudab see metalli äärmiselt tugevaks,
mistõttu mõõga saab teritada väga teravaks
ning mõõk ka püsib teravana. See voltimisprotsess
annab jaapani mõõgale ka oma spetsiifilise mustri,
hada. Tugev teras on aga habras ning kipub tugevama löögi
puhul purunema. Seetõttu kasutatakse mõõga
südamikuna madala süsinikusisaldusega pehmet metalli
shingane’t, mille ümber mähitakse kawagane või
hagane, kõrge süsinikusisaldusega teras, mis on valmistatud
tamahaganest (ülalkirjeldatud meetodil), ning surutakse need
kihid kokku. Liitmisprotsessi kutsutakse tsukurikomi’ks.
Peale kokkusurumist ning enne karastamist kaetakse tera spetsiaalse
saviga, yakiba-tsuchi’ga. Lõiketera lähedale
pannakse vähem savi ning mõõga külgedele
ja taha rohkem savi. Nii karastub lõiketera kiiremini,
muutes terase pindmise kihi ülitugevaks martensiidiks, mis
on veelgi tugevam kui pindmine sepistatud metall, paksu ja õhukese
savikihi üleminekupiir ongi karastuspiir, ehk hamon.
Karastamine
Kui tera on saviga kaetud, algab pihta tõeline metallurgiline
kirurgia. Kui terase temperatuur ületab 726 kraadi, toimub
terase struktuuris metamorfoos ja selleks, et ilmuks hamon, on
vaja teras kuumutada üle metamorfoosipunkti. Samas aga raua
kristall laieneb liigselt, kui kuumutada terast üle 800 kraadi.
Kõige tugevamaks muutub teras, kui seda kuumutada 750-760
kraadini. Sepp peab oma kogenud silmaga ära tundma hetke,
mil terase temperatuur on kõige optimaalsem, seepärast
viiakse kuumutamise protsess läbi pimedas ruumis. Väidetavalt
on tänapäeva inimeste silmade tundlikus tänu rohkele
tehisvalgusele muutunud mõnevõrra väiksemaks,
mistõttu on ka kaasaegsetel seppadel raskem näha orani
punase konkreetseid spetsiifilisi toone, mis viitaksid õigele
temperatuurile. Samuti sõltub mõõga kuumutamise
temperatuur loomulikult ka koolkonnast, meetodist ja kasutatud
materjalidest ning võib seetõttu kõikuda.
Kui
teras on saavutanud optimaalse temperatuuri, kastetakse see vette
– lõiketera karastub silmapilkselt ning selle pinnale
tekib martensiidikiht mis on äärmiselt tugev, kuid ka
suuremate kristallidega. Kuna lõiketera kristallid kasvavad,
aga tagumise metalli kristallid ei kasva, siis tõmbub tera
iseenesest kergelt kaardu. Saviga määrimisel on kaks
eesmärki – esiteks erinev karastusaste ning teiseks
jahutamise kiirendamine. Kui lõiketera osa mitte katta
õhukese savikihiga, siis ei oleks karastusprotsess nii
kiire, kuna vesi aurustuks teraga kokkupuutel silmapilkselt, ning
ülikuum tera tekitaks enda ümber põhimõtteliselt
aurupadja, mis takistaks vee juurdepääsu. Antud spetsiaalsavi
on aga täis kapillaare, mis tõmbavad enda sisse vett.
Vesi muutub teraga kokkupuutel õhumulliks, mis tõuseb
ülespoole, tekitades ruumi uuele veele ning luues põhimõtteliselt
ringluse, mis tagav vee võimalikult kiire kokkupuute terasega.
Karastusprotsessi tulemusena ilmub nähtavale pindmine teraline
struktuur – suuri terasid kutsutakse nie’ks ja väikeseid
terasid nioi’ks. Antud terad kohtuvad omavahel karastuspiiris.
Terad ilmuvad nähtavale kui tera vaadata ca 20-30 kraadise
nurga all vastu valgust – seetõttu peab hamon’i
vaatlemiseks tegelikult võtma tera kätte. Muuseumides
olevate mõõkade karastuspiir pole reeglina ehtne
ning on terale kosmeetiliselt lisatud. Suurte ja väikeste
terade segunemine hamon’is aitab muuta mõõga-tera
ka vastupidavamaks, kuna muudab ülemineku pindmise martensiidikihi
ning pindmise terase vahel sujuvaks, sujuv ülemineks aitab
amortiseerida mõõgale mõjuvaid jõudusid.
Järsk üleminek muudaks mõõga murdumise
või surmava pragunemise märksa kergemaks. Mis puudutab
sori’t, ehk kurvatuuri, siis karastamine küll tõmbab
tera kõveraks, kuid reeglina on karastusest tekkiv kurvatuur
liiga väike, ning sepp painutab omakorda tera sori suuremaks.
Karastamisele ning kuju viimistlemisele järgneb teritamine
ja poleerimine, mille viib läbi togishi, mõõgapoleerija.
Mõlemad protsessid viiakse läbi spetsiaalsete kivide
abil. Alles peale poleerimist muutub nähtavaks mõõga
karastuspiir, struktuur, ning kõik muud detailid.
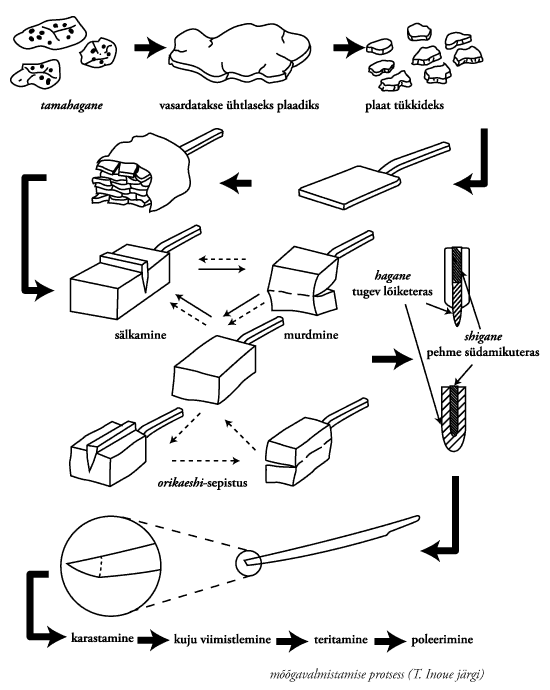
|